PRODUCTS / PARTS / TEKNIKA CRANKS | TEKNIKA PEDALS | TEKNIKA STEMS
TEKNIKA STEMS
7075 Aluminum | Titanium | Cerakote
These 7075 Al stems use a constrictor system. The two wedges push back into the steer tube, grabbing it nearly all the way around rather than just pinching at the bolt. This is not only more secure, it allows for an even lighter overall weight. We have two models, one for 31.8mm handlebars that comes in 38mm and 50mm lengths, and one for 35mm diameter handlebars that comes in 42 & 50mm. Available in custom Cerakote colors – SEE CERAKOTE COLOR SWATCHES
- Constrictor system pinches AND wedges for full squeeze
- Flip it for a 10mm lower stack height
- 31.8mm Bars / 38 & 50mm Reach / 106g & 122g
- 35mm Bars / 42 & 50mm Reach / 128g & 148g
$150-200.00 USD
PRE-ORDER NOW FOR AUGUST PRODUCTION RUN
$50 DEPOSIT
CHOOSE YOUR CUSTOM COLORS – We have 18 stock Cerakote colors or you can select PICK MY OWN COLOR and we will contact you to match any color you want. – SEE COLOR CHART
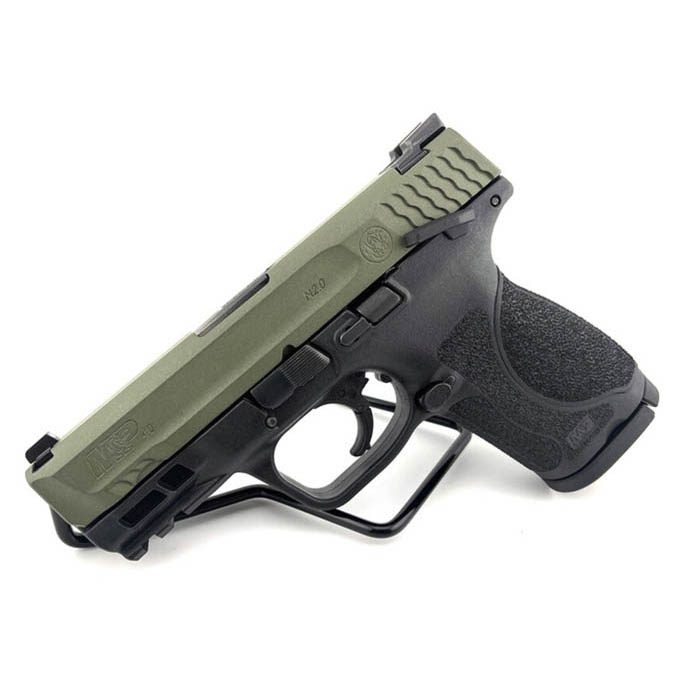
Cerakote Ceramic Coating
Cerakote is a high-end ceramic finish that was developed for the extremely high demands firearms industry. It offers industry leading durability, hardness, and scratch resistance, as well as chemical resistance, that will protect the overall finish of your bike. Cerakote is not prone to the chipping and blistering commonly found in existing paint finishes, and is not affected by chemicals such as road oil and tar, chain lube and brake fluid.
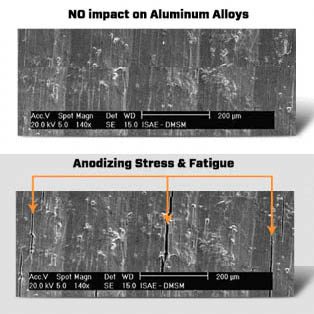
Cerakote Vs. Anodizing
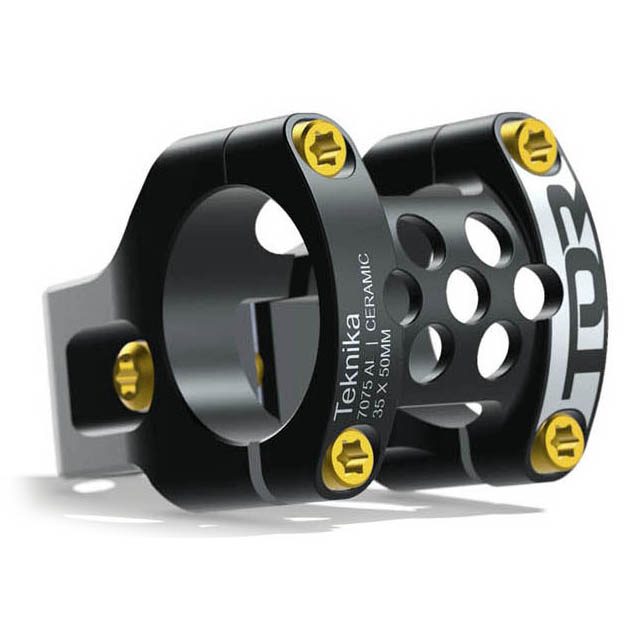
Stock black/silver/gold
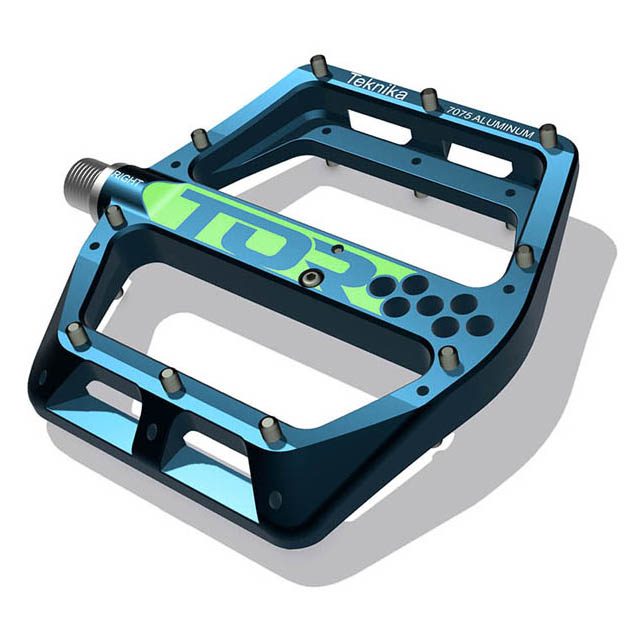
Custom color options
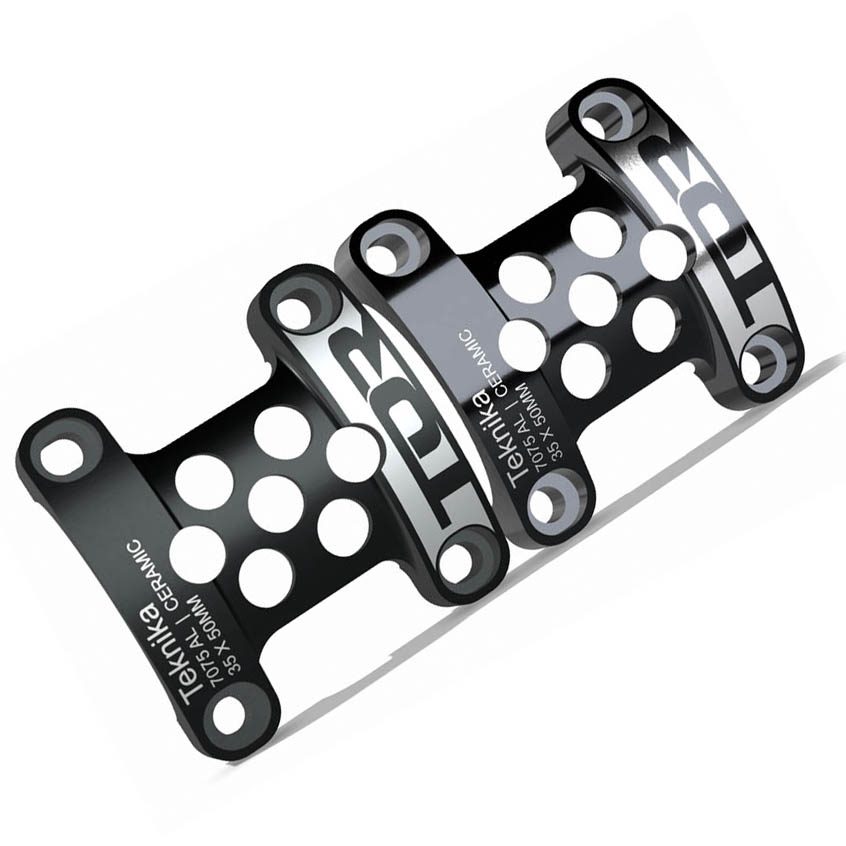
Matte or gloss
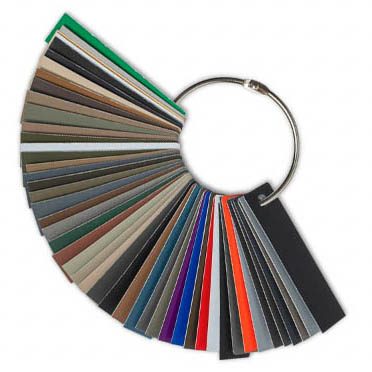
Go nuts!
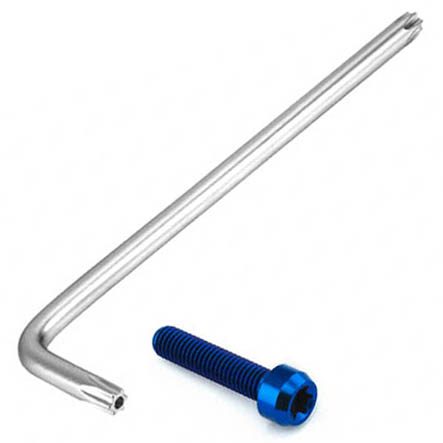
T-30 Torx fittings
Custom Color Chart
These are our custom color options. If you want something that we don’t have here, just let us know and we can quote you. If you want some inspiration, check out our friends at Daylight – www.daylightcycles.com/finishes/
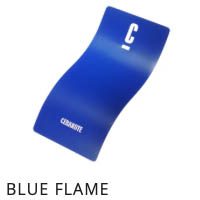
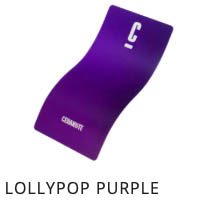
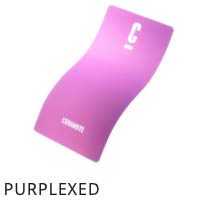
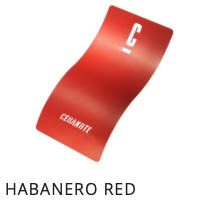
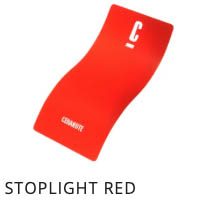
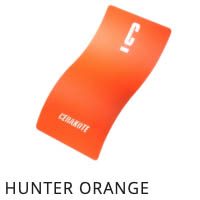
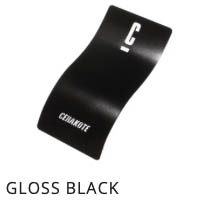
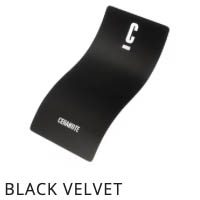
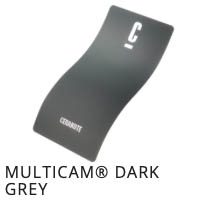
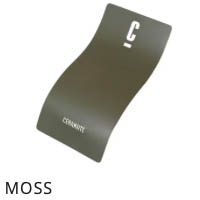
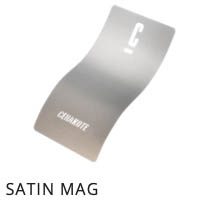
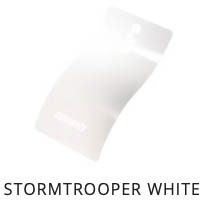
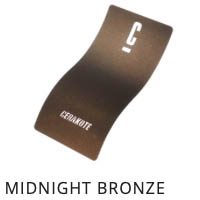
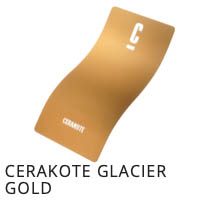
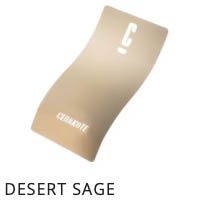
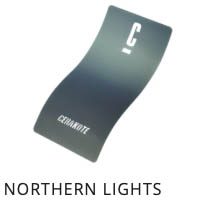
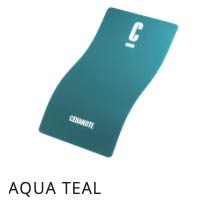
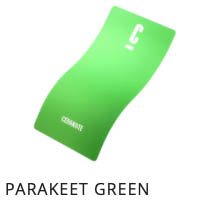
Teknika Development
The Teknika products (1) start with a premise and concept; either something patently different or a twist on something that hasn’t been taken as far as it can go. Then (2) we spend a lot of time working this out virtually in Shapr3D which is a fantastic industrial design program that fully integrates with Solidworks and CAD/CAM software. Once we have something we believe is a solid concept, we (3) 3D print it in carbon composite with our Markforged Mark II printer. The print isn’t quite strong enough to ride, but we can mount it to a bike and check fit and function. From there, (4) we go to CNC machined samples to ride test. Changes and iterations are done throughout the process. Once we settle on a finished design, we (5) create final samples that go through a full run of industry standard testing.
Here are some images of the development of the cranks. Click here to see a video of a carbon 3D print